I bet you have brushed your teeth the same way every day for a long time.
You have a process that you follow for brushing your teeth.
You also have processes for showering or bathing or putting on your clothes, cooking, shopping and going to sleep.
I challenge you to think of anything you do regularly that does not involve a process.
The same applies to work. Everyone in an organization uses processes to achieve the results expected of them.
Definition of a process
The actions undertaken to achieve a wanted outcome.
If I had a skeleton of a process it would consist of free moving blocks with spaces between them
all lined up.
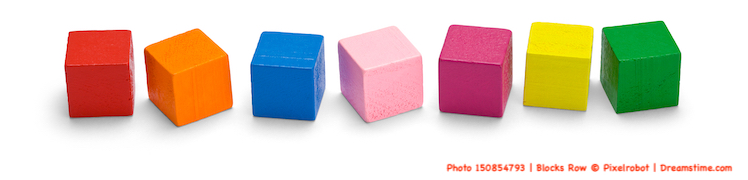
Each block represents an action that changes something about whatever is flowing through the process. The following are examples:
Process: APPROVAL FOR PAYMENT. What flows through are documents and information.
Process: ASSEMBLY. What flows through are parts.
Process: LATTE COFFEE. What flows through are ingredients.
Generally, what flows through processes are things and data, either alone or in combination.
Each action step makes changes to data or things.
The OUTCOME is what the purpose of the process is.
The actions are designed to produce the desired outcome, over and over again. Provided the process is followed each outcome will be the same. If the outcomes from such a process are what you want (quality) it is called a CAPABLE PROCESS.
Journey to a Perfect Process
The worst type of process is one that does not give you a consistent outcome but, rather, gives you randomly a quality outcomes and non quality outcomes. Such a process is called UNSTABLE. In fact an unstable process is multiple processes – one that produces quality and one or more that produce non quality.
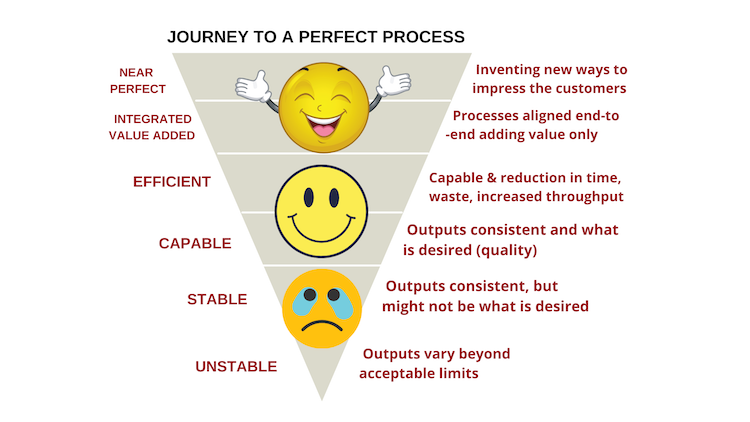
UNSTABLE processes are at the bottom of the hierarchy of processes.
In order to improve an unstable process the first step is to stabilize it. In practice that means to do your best to decide on each of the actions and then get them to be followed. In this way you know exactly was has been done in the process. The outcome might not be what you want, but if it is consistent then it is a stable process.
A STABLE PROCESS produces the same outcome each time, even it is non quality. The value of a stable process is that you know that somewhere in the process is the cause of the non-quality outcome.
When you unearth the possible cause and test a solution that eradicates the cause and it works then you have a stable process that produces quality outcomes. That is a CAPABLE process.
Even a CAPABLE process has room for improvement in that there might be multiple instances of waste in the process. At a high level we look at three types of waste – Non value added actions, waiting time or wasted time, rework. Eliminating waste leads to an efficient and capable process.
It is only at this stage that consideration should be given to automation. Trying to automate an unstable process as a solution to non-quality outcomes is wasted and expensive effort.
Once waste had been drastically reduced the process that remains can be aligned end-to-end using value added actions only. INTEGRATED, VALUE ADDED only processes still have opportunities for improvement – using technology, simplification, redesign of touch-time work as examples.
As a MM you will have multiple processes at work in your area of responsibility.
Always start with focusing on non-quality outcomes as determined by the customer. The ‘customer’ might be the end customer or the next department or person in the process.
MM’s and processes
Choose to work on what you consider is the biggest issue and gather a few of the people actually doing the work in the process and have them do the following in order:
1. Speak to the ‘customers’ of the process to determine their needs and how the process is currently doing in meeting them. Choose the biggest, most often occurring, problem of the customer.
2. Map the process at a high level (5 – 8 steps) and obtain data on how the process is working. The team might have to actually measure the process if this data is not readily available.
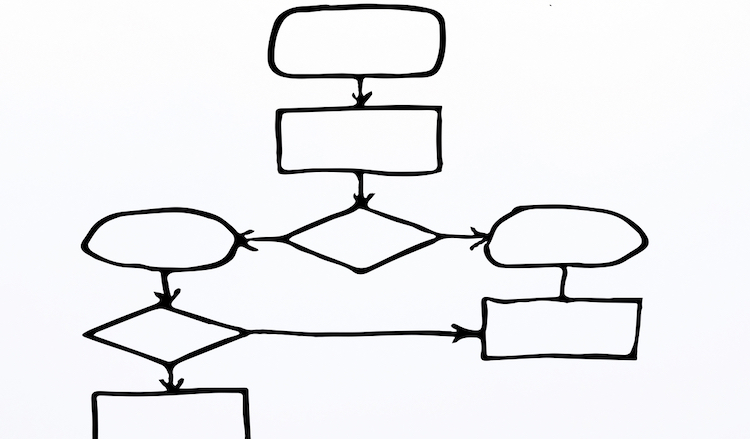
3. Compare the outcomes of the process with the customers issues and select the most prominent non-quality outcome to fix.
4. Study the map of the process and answer the question – where about in the process are things going wrong that are possibly causing the non-quality outcome? When you have a possible answer to the question, design an experiment to test whether resolving the issue will solve the customer problem identified.
5. Only if the cause has been proven to be the root cause, do you develop possible solutions to be implemented.
6. Finally implement the changes needed until they are being done as the new way of doing things. Measure that the problem was solved once the process has settled down. If not go through the process again until solved.
7. Select another customer issue to resolve.
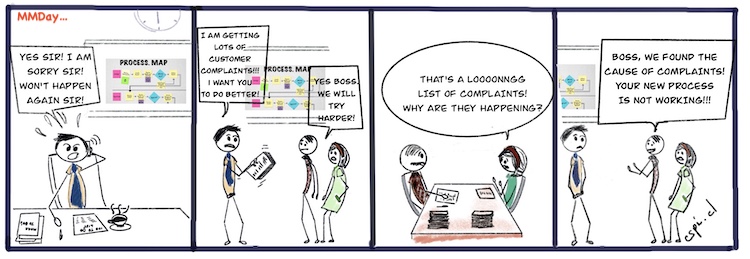
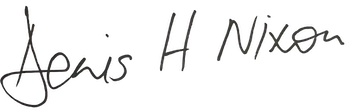